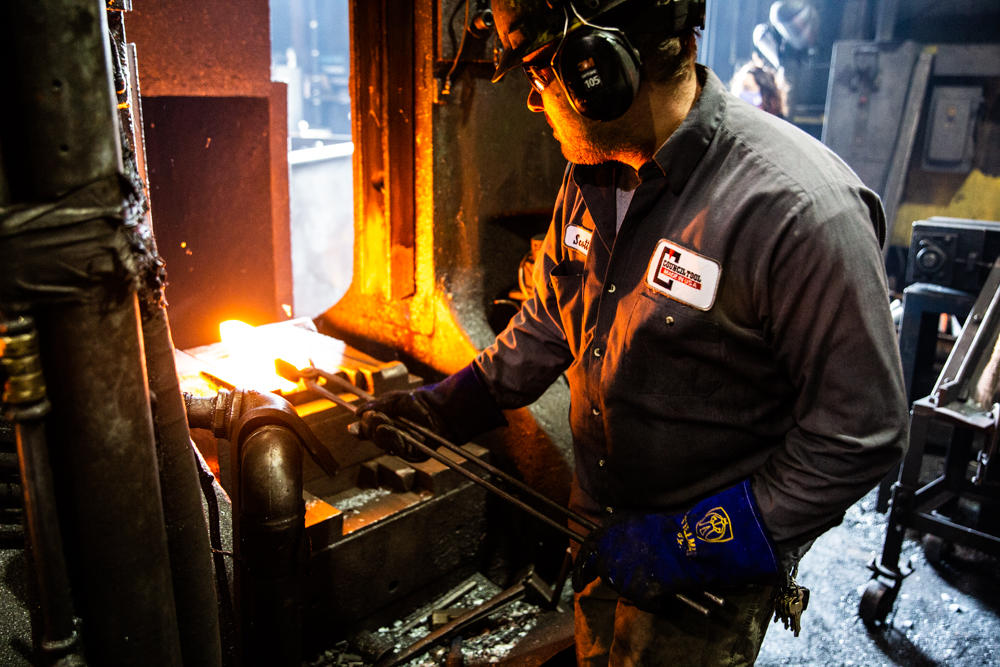
Drop forging and casting are both processes used in metalworking to create components, but they differ significantly in terms of their methods and outcomes. Let’s compare the two processes and highlight why drop forging is often considered superior:
- Process:
- Drop Forging: Drop forging involves shaping metal by hammering it between two dies. The metal is heated to a malleable temperature and then hammered to conform to the shape of the dies. This process is typically used for high-strength metals and produces parts with excellent mechanical properties.
- Casting: Casting involves pouring molten metal into a mold, allowing it to solidify, and then removing the finished part from the mold. Casting can be done using various methods such as sand casting, investment casting, or die casting.
- Material Properties:
- Drop Forging: Drop forging typically results in parts with superior mechanical properties compared to cast parts. The repeated working of the metal during forging aligns the grain structure, making the part stronger and more resilient to fatigue and impact.
- Casting: Cast parts may have less uniformity in grain structure and may contain defects like porosity, shrinkage, or inclusions, which can weaken the part and reduce its mechanical properties.
- Precision and Complexity:
- Drop Forging: Drop forging allows for the creation of complex shapes with high precision. The dies used in drop forging can be intricately designed to produce parts with tight tolerances and intricate geometries.
- Casting: While casting can produce parts with intricate shapes, it may not achieve the same level of precision as drop forging. Additionally, casting may require more post-processing to achieve the desired dimensional accuracy.
Overall, drop forging is often preferred over casting for applications where superior mechanical properties, precision, and surface finish are required. While casting may be suitable for certain applications where cost or complexity considerations outweigh the need for high mechanical properties, drop forging remains the preferred choice for many industries, particularly in sectors such as aerospace, automotive, and defense.